Repair Cracked Cases
Text and Pictures by Mark Trotta
When confronted with a cracked engine case, the motorcycle restorer has two options, find a replacement or have the case welded. To repair cracked cases correctly, the motor needs to be stripped down, then the cases have to be made spotlessly clean. The final step is the most important, and that is to find a qualified welder.
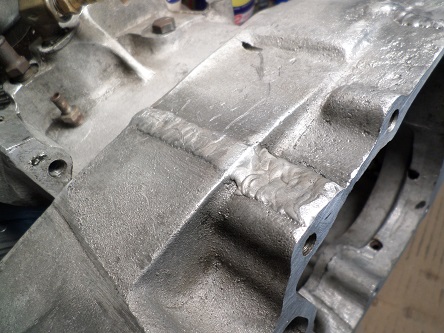
Best Way To Repair Cracked Engine Cases
Aluminum engine cases can be Stick welded, MIG welded, or TIG welded. They can also be gas-welded by a process called aluminum brazing.
The Problem With Welding Aluminum
Because of the high thermal conductivity and low melting point, distortion and burn-through are common when welding aluminum cases. By trying to weld smaller and less penetrating beads, the distortion will be less, but the repair is weaker.
Different Types Of Aluminum Alloy
There are many different types of aluminum alloy. Motorcycle engine castings are often a combination of aluminum/silicon cast, or a cast-iron alloy, or a pressure die-cast aluminum. Some are a good quality and others are very porous. Some castings aren't very weldable.
Before getting your engine case repaired, try to find out which type of alloy your engine cases are. Pre-Evo Harleys (before 1984) and vintage German and British bikes have a good quality alloy.
In more recent times, an inferior quality of aluminum was used in some year Harley Evo engine cases. Older Japanese motorcycles generally have poor quality aluminum.
_________________________________________________
_________________________________________________
Another concern when welding an aluminum engine case is, if the weld repair is close to a mating surface, there is a high risk of warpage. A delicate balance of heat versus size is needed.
**********************
TIG Weld Engine Case
Today, the most popular process to repair aluminum cases is TIG welding. Not only is it mechanically strong, it's also visually appealing. However, TIG welding thicker aluminum, like engine cases, is considerably more time-consuming, which equates into more labor and a higher shop bill.
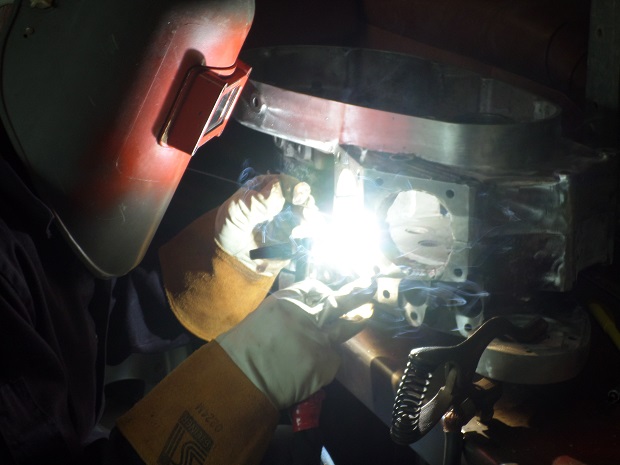
**********************
Stick Weld Engine Case
The principal advantage of using the Stick or Arc welding process is that a highly concentrated heating zone is obtained with the arc. The procedure of using brazing rods for repairing aluminum wheels is quick, long-lasting and fairly easy.
Stick welding engine cases is a viable alternative to TIG welding. If performed correctly, excessive expansion and distortion of the aluminum is prevented and the end result will be an oil-tight engine.
**********************
MIG Weld Engine Case
MIG welding is a fast, adaptable process, but to weld a thick aluminum alloy, a large 220v machine with DC reverse polarity is required.
Additionally, an inert gas is required, such as welding-grade argon, helium, or a mixture of these. A common mixture of approximately 75% helium and 25% argon provides the advantages of both shielding gases without the undesirable characteristics of either. The aluminum oxide film on the case must be removed prior to welding.
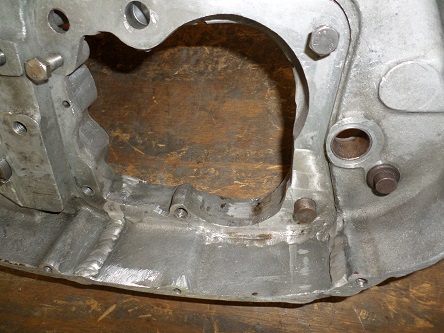
**********************
Aluminum Brazing
Although I have personally never used aluminum brazing, it is an alternative to Stick, MIG, or TIG welding. This procedure uses an alloy rod which, when properly heated and treated, will bond to aluminum similar to the way tin solder bonds to copper or steel. Unlike epoxy, the alloy bonds to the aluminum. This creates a metal repair which can be machined and can withstand impact.
Because of the low heat input required and flux build-up, aluminum brazing will not always be the best solution. It cannot be used to replace chunks of missing aluminum.
**********************
Prep Before Welding
Remove surface oxides with a stainless steel wire brush (used only for aluminum) or a strong alkaline or acid. You can also try a oxide-removal solution, which are offered in spray or squeeze bottles. Be careful handling these solutions. Rinse and dry the part before welding.
Keep the aluminum dry and at room temperature, and weld within a few days of cleaning. Clean the cases again if it isn't welded within that time.
Clean, Clean, and Clean Again
If the damage is in an area that is exposed to hot oil, proper cleaning is essential. When you drain the oil, some of it stays in there stuck to stuff because that's what its designed to do. The case must be cleaned well. Heating them to about 250 degrees will bring the oil to the surface. If the crack is being repaired from the inside, it needs to be exceptionally, spotlessly clean for anything to stick to it.
Cast aluminum that has been soaked in oil, makes them difficult to weld. Welding dirty aluminum is futile.
_________________________________________________
_________________________________________________
Engine and transmission cases can be difficult to get clean enough to properly weld. Kerosene is a good cleaner to flush out the crankcase, because its a thin solvent but still a lubricant.
Aluminum and aluminum alloys should NOT be cleaned with caustic soda or cleaners with a pH above 10, as they may react chemically. Use an organic solvent such as acetone, a citrus-based degreaser, or a strong soap. Rinse with hot water and dry thoroughly before welding.
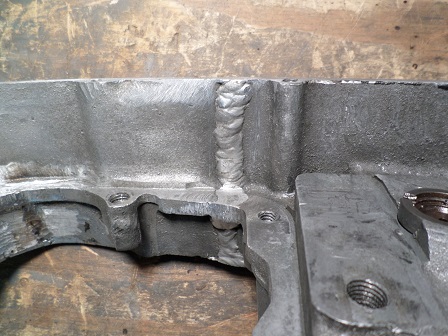
No matter what process you use to clean them, engine cases will often ooze oil from the pores of the metal when heated. It will sometimes take several cleanings to get to the point where you could weld them properly.
Pre-Heat Cases
Preheating an aluminum engine case before welding reduces the chance of cracking. Preheat temperature should not exceed 230 degrees Fahrenheit. A temperature indicator, like a temperature stick, should be used to prevent overheating. Remember, aluminum doesn't glow like steel does when heated.
_________________________________________________
_________________________________________________
After Welding
As the aluminum cools down after the welding process, it both contracts and solidifies simultaneously. This means that a thin area gets to solid state faster than the thick areas near it, and that's when the stress gets introduced into it. So the welding may add new stresses, and the thin area in now under tension.
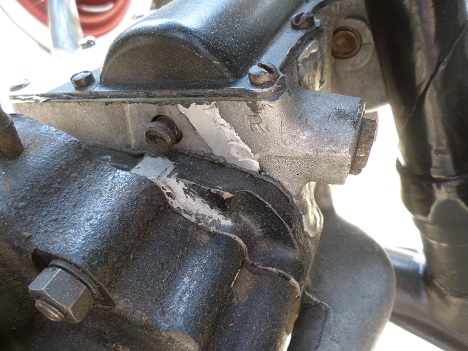
After the cracked engine case is repaired, there may be some distortion. Check the case edges and mill or file flat if needed.
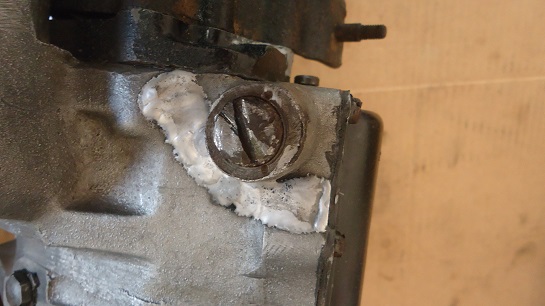
**********************
On V-Twin engines, if non-original flywheels and rods are being fitted, line boring or honing should be performed. This will correct any misalignment and prevent rapid bearing wear.
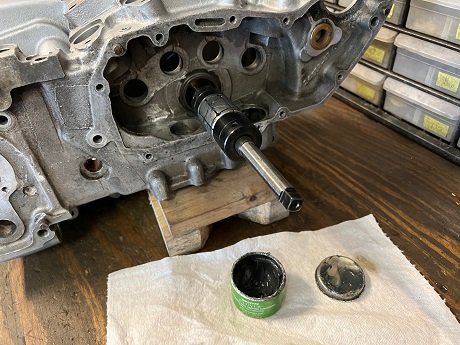
Read: Harley Crankcase Lapping Tool and Usage
**********************
Electric rotary grinders make quick work of grinding down weld repairs.
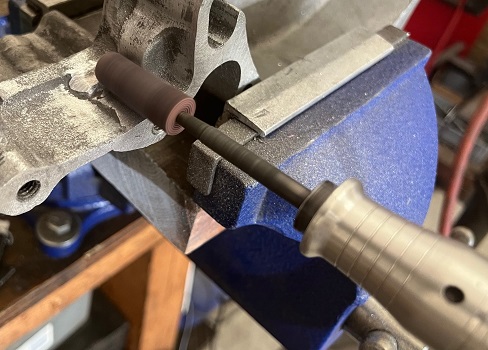
Smoothing a weld on aluminum with an 80 grit sanding drum
Read: Foredom Rotary Shaft Tool Review
Once engine cases are repaired, they are as good as new - provided the repair was done right. Don't entrust this job to someone whose only qualifications are that they own a welding machine. Trying to save money here is false economy - a welder with good intentions can make the damage worse than it is. Find someone who is experienced at welding cast aluminum and have it repaired correctly.
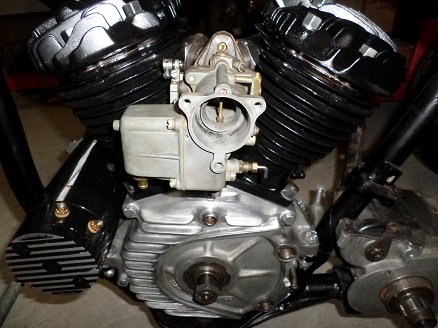
**********************
Related Articles: