Motorcycle Engine Tools
text and pictures by Mark Trotta
Aside from basic hand tools and a torque wrench, engine building tools include gear pullers, snap ring pliers, a piston ring installer, and some other specialty tools for your make and model.
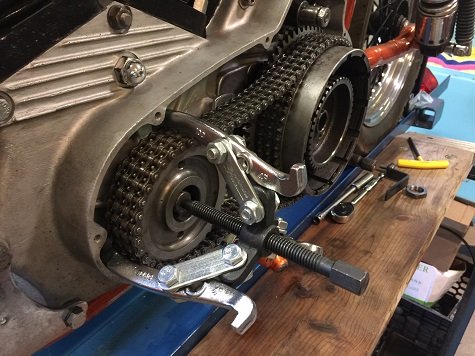
One of the first steps of a proper engine build is inspecting and measuring old and worn parts.
For article on Measurement Tools For Engine Builders click here.
********************
Piston Pin Puller
If you work on different types of engines, you'll make good use of a Motion Pro Piston Pin Puller.
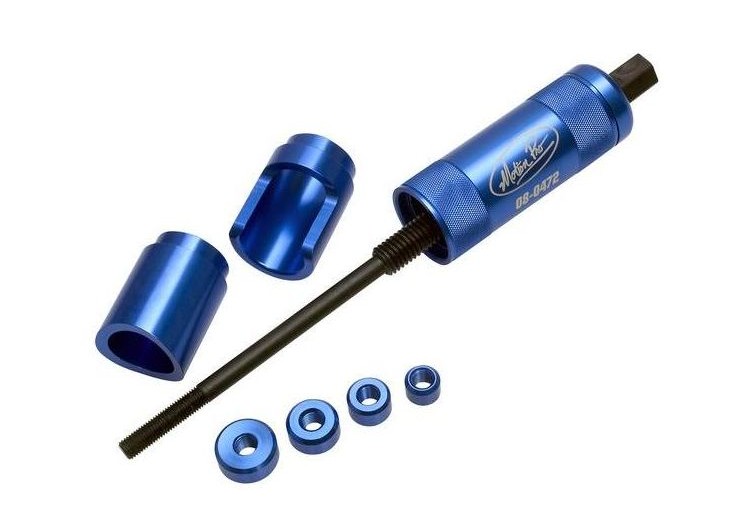
It features interchangeable piston adapters and fits all piston pins from 12mm (1/2") to 24mm (1").
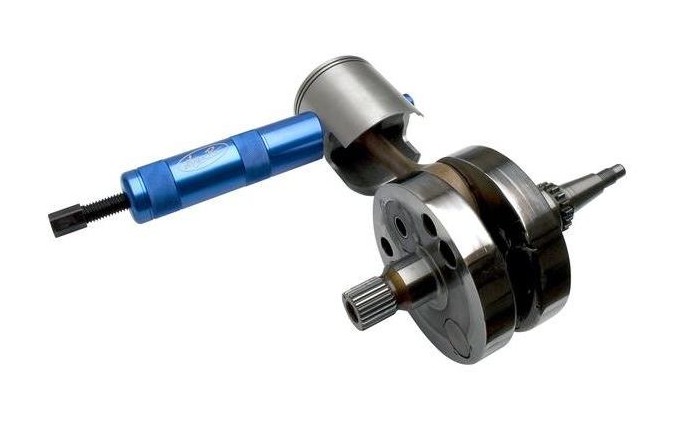
Works on both full skirt and short skirt slipper pistons. Also features non-marring aluminum pin adapters.
********************
Piston Ring Expander
Don't be tempted to install rings into piston grooves by hand. It's a bad idea, because rings get deformed by the twisting action, which may cause sealing problems. A piston ring expander is an inexpensive tool.
Shop: Piston Ring Spreader Tool
Piston Ring Installer
To install pistons and rings back into the cylinders, a piston ring installation tool is needed. A clamp-style ring compressor is the least expensive style, but consider investing in a piston ring installer set. Most sets includes a half a dozen popular sizes you can use for other engine projects.
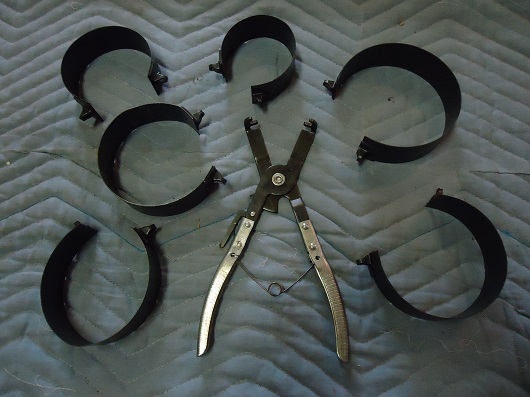
Shop: Piston Ring Compressor Set
********************
Valve Spring Compressor
This is the tool you need for removing and installing valves and valve springs. Although it was designed to fit pre-Evo Harley Big-Twins and Sportsters, it's really a universal tool.
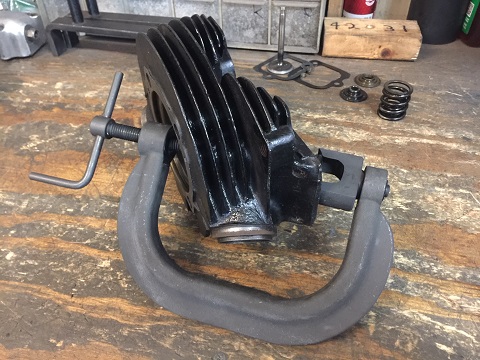
Shop: Valve Spring Compressor
The one in the picture is a V-Twin 16-1788. It's a copy of the Harley-Davidson tool #96600-36.
********************
Gear Pullers
Removing gears usually requires a gear puller. Three-Jaw gear pullers are offered in different sizes.
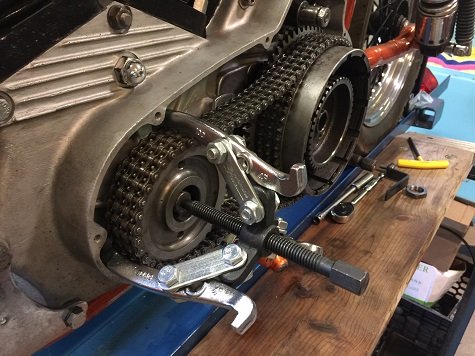
Having several gear pullers in your tool box gives you more versatility.
********************
Cylinder Boring and Honing
If you're restoring an old motorcycle engine, boring a cylinder back to round may require removing anywhere from .003" to .010" or more of metal. Professional machine shops have large, expensive, dedicated machines to perform all kinds of cylinder boring.
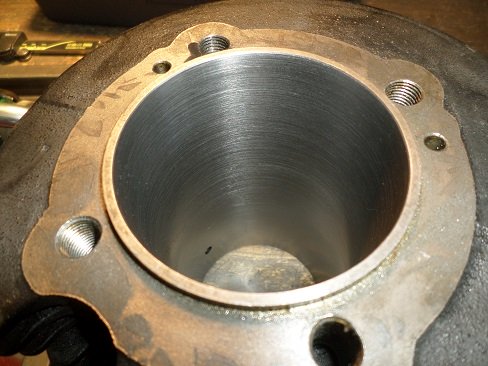
The same process can be done in your home garage, but will take considerably more time.
The tool I use is a Lisle 15000 which services 3" to 4-1/4" cylinders. It is a rack-style and has two stones and two wipers which clip on and off. There is a universal-joint between the handle and the head. After hooking it up to your 1/2" drill, press the trigger and the tool starts rotating, which expands the tool head to the cylinder size.
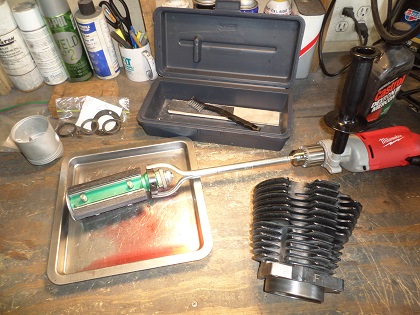
By using a Lisle rigid honing device and a slow-speed drill, high-quality motorcycle engine cylinder boring is possible.
Read: DIY Motorcycle Cylinder Boring
********************
Snap Ring Pliers
If you're rebuilding an engine or a transmission, snap ring pliers are a must-have tool.
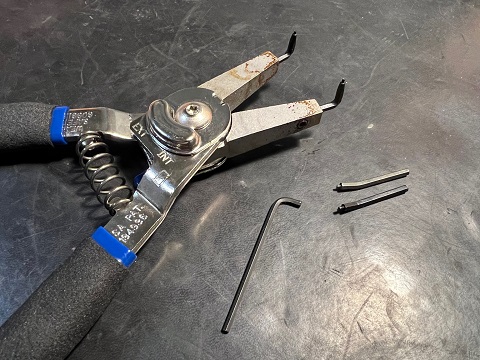
Convertible snap ring pliers can be used for either internal or external E-clips. Most good brands (like Channellock) come with an assortment of tips.
********************
Slide Hammer Set
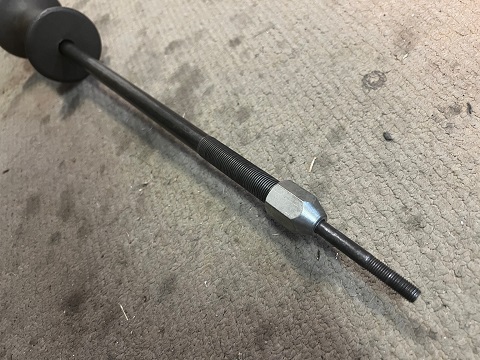
Shop: Slide Hammer Puller Set
********************
Tap And Die Set
If you're working an old motorcycle that's been neglected, I would rate a tap and die set as a necessity.
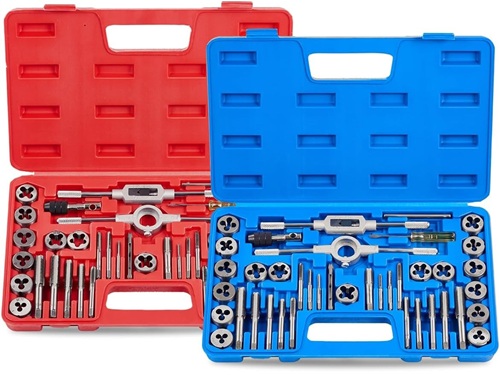
With proper technique and lubricant, taps and dies will cut mild carbon and alloy steel, cast iron, aluminum, brass, and bronze.
********************
Torque Wrench (Foot-Pounds)
For those who haven't used a 'click-style' torque wrench before, you set the desired value on the handle scale, then begin tightening the fastener. When the preset torque value is reached, the wrench will emit a "click" that will be heard and felt.
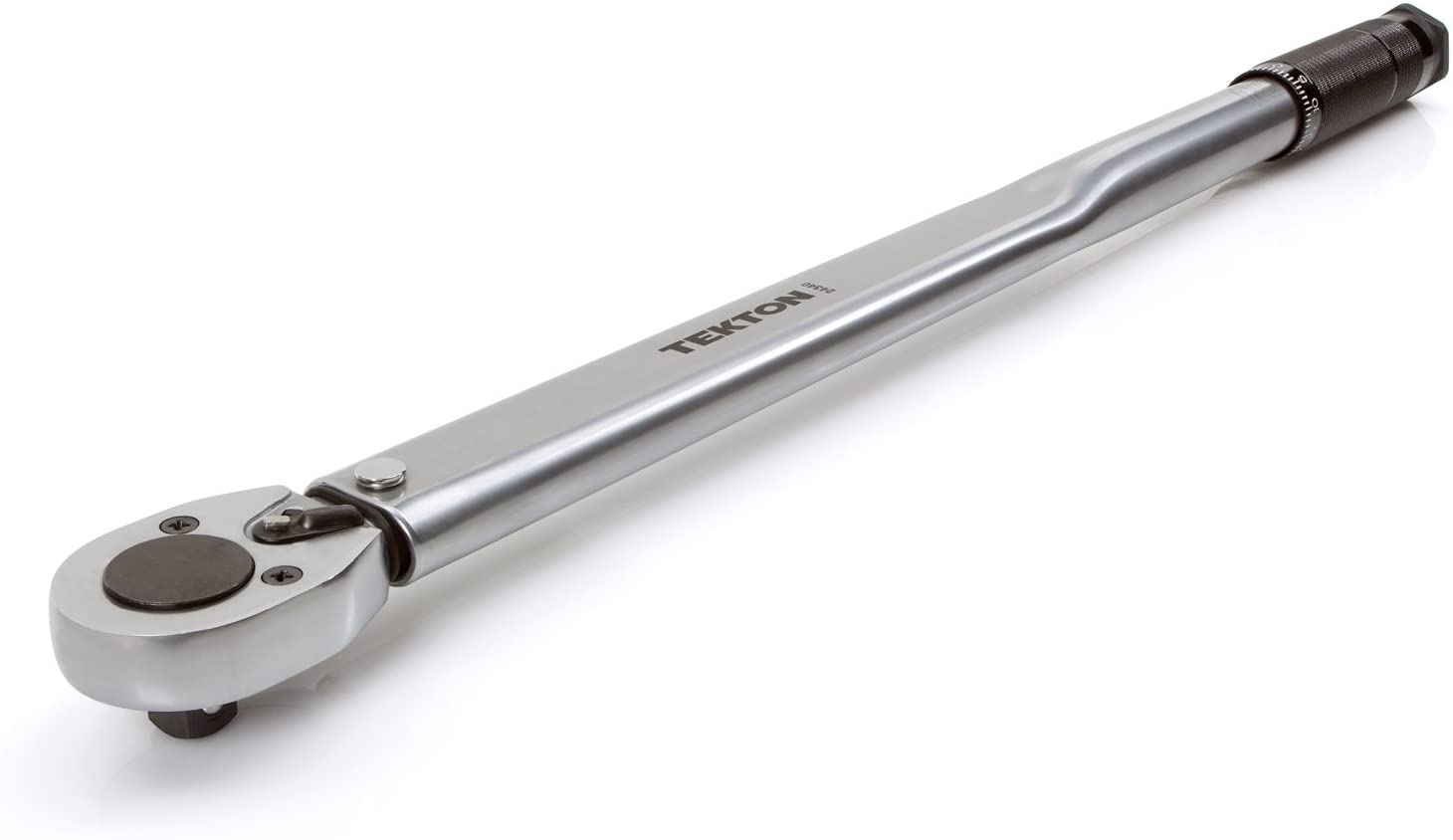
Shop: 1/2" Torque Wrench (10-150 ft/lbs)
A 1/2" drive torque wrench will generally cover your needs up to 150 foot/pounds. It is recommended to torque bolts in increments; example, first pass 20 ft/lbs, then 40 ft/lbs, then 60 ft/lbs, etc. until desired torque value is reached.
Stay away from beam-style torque wrenches. Most are inaccurate, and all of them hard to read while you're using it.
Torque Wrench (Inch-Pounds)
On the lower end of the scale are 1/4" drive torque wrenches. These are nice to have for oil drain plugs and smaller bolts that require less torque.
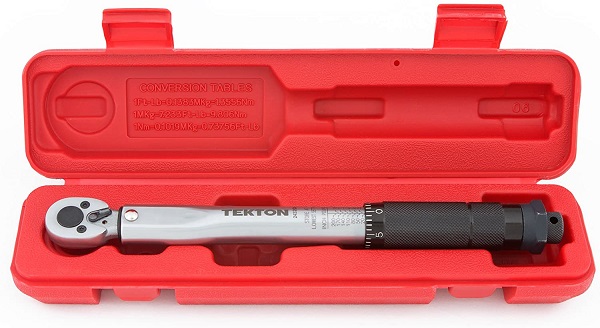
Shop: 1/4" Torque Wrench (20-200 in/lbs)
********************
Specialty Tools
Every type of motorcycle engine will require a specialty tool or two. The tool in the picture below is for installing piston lock-rings in early Harley-Davidson 45 flatheads. It lightly stretches the lock ring just enough to fit into the groove. The factory part number for this tool is 12052-32, and it's primary use is for 1932-1956 Harley-Davidson 45 models, but works for some other models as well.
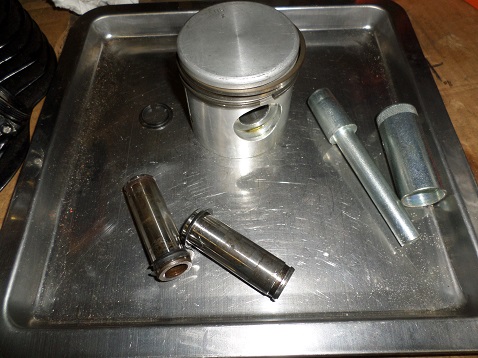
********************
Harley Pinion Shaft Honing/Lapping Tool
Honing/lapping motorcycle engine cases assures precision alignment of flywheel shafts.
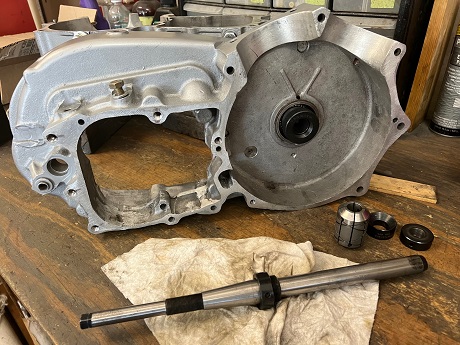
This tool fits Harley Big-Twins 1955-1998 and Ironhead Sportsters 1957-1976. Also fits Harley Flathead UL models 1937 through 1948.
Read: Harley Crankcase Lapping Tool and Usage
********************
DIY Engine Tools
If you don't have all the tools needed for your motorcycle engine build, you can either borrow them or buy them (new or used), but many can be fabricated. If you can cut, drill, and weld metal, consider making some the tools yourself.
Read: DIY Motorcycle Tools
Flywheel Truing Stand
After a Harley V-Twin flywheels are rebuilt, they need to be trued before being reinstalled into the cases. For this, you'll need either a lathe or a flywheel truing stand. A $900 truing stand is a nice luxury, but homemade units work just as well.
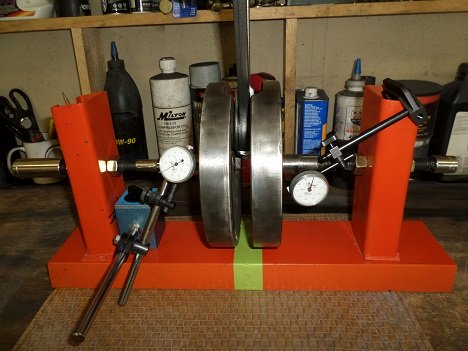
Read: DIY Flywheel Truing Stand
********************
Harley Ironhead Engine Tools
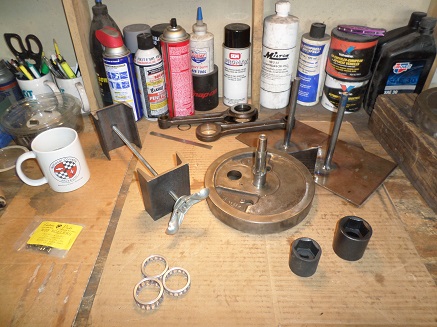
Read: Ironhead Specialty Tools
********************
Camera
Taking pictures before and after is extremely helpful during re-assembly. A digital camera is nice to have, but a smart-phone works just as well.
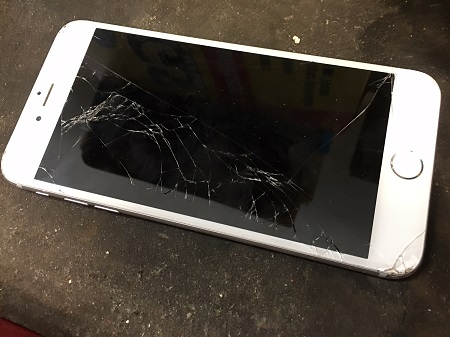
TIP: Put a with a screen protector on your phone!
********************
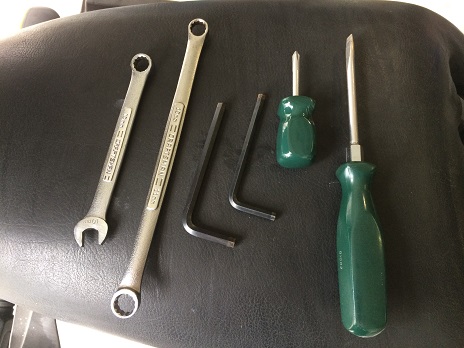
Read: Best Hand Tools
********************