How To Polish Aluminum Engine Parts
Article by Mark Trotta
Polishing aluminum engine parts is always a better choice than chroming.
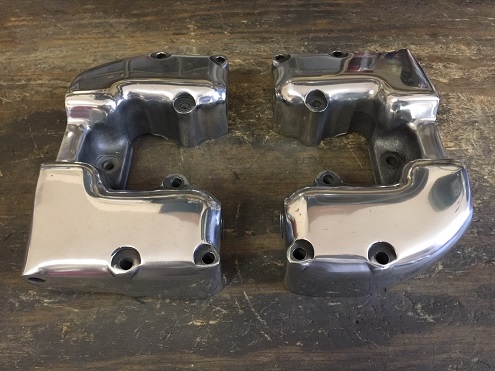
Not only does chrome plating hold in engine heat, it pits and flakes over time.
************************
To read about how to polish aluminum motorcycle forks click here.
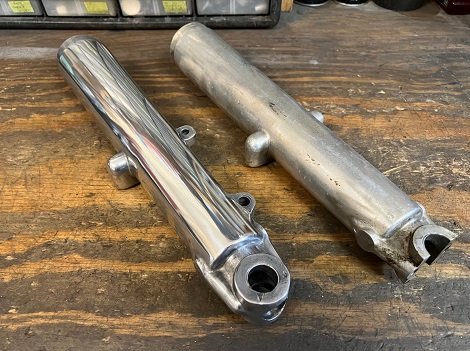
************************
Removing Chrome From Aluminum
There really is no easy or safe way to remove old chrome in your home workshop.
I sent the primary cover, cam cover, and rocker boxes from my 1962 Sportster to a plating shop (Brown's Plating, no longer in business) to have the chrome chemically removed.
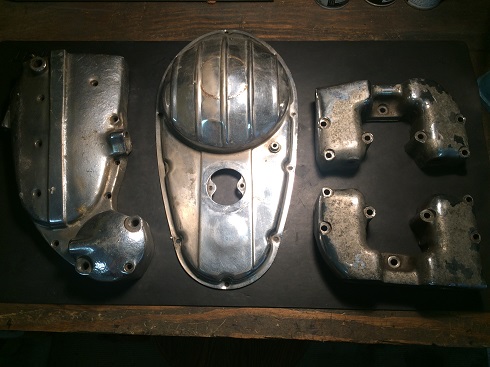
Six weeks later, the parts arrived in raw metal form. I began working on the rocker box that had the heaviest corrosion first.
************************
Steps Before Polishing
Depending on how badly the aluminum is pitted, they'll be 3 to 5 steps of filing and sanding before going to the buffing wheel.
First, there's filing to get out any deep pits or grooves. Next is the sanding to remove all the filing scratches, and make the finish uniform.
- Filing
- 50 Grit Emory cloth
- 80 Grit Emory cloth
- Fine Emory cloth
- 240 Grit wet sand
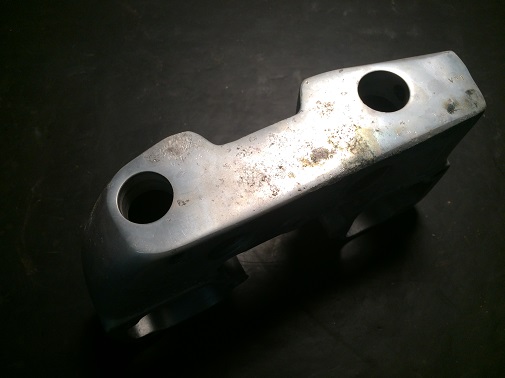
Filing Aluminum
Because the depth of some of the pitting, I started with a 12" course metal file.
NOTE: Aluminum is a soft metal and is easy to over-file.
When filing aluminum, you don't need or want to apply much pressure--let the file do the work. You only want to remove enough metal to get to a flat, level surface.
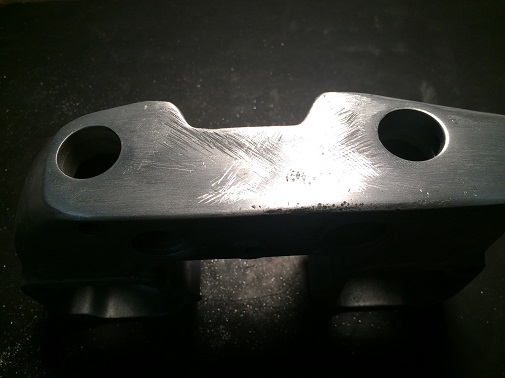
Work slowly and evenly.
Notice the diagonal (45 degree/135 degree) swipes left by the metal file. This is to offset the left-right filing, which helps keep the surface flat and even.
Next step is sanding.
Starting with a hand-held piece of coarse Emory cloth, "check" or cross-hatch the surface left and right, and then up and down.
The check marks give you a visual of how much you've sanded off, so you don't sand down too far (or not far enough) in one area.
TIP: Stop periodically and hold the work up to the light at different angles. This gives you a better perspective of the entire work-piece.
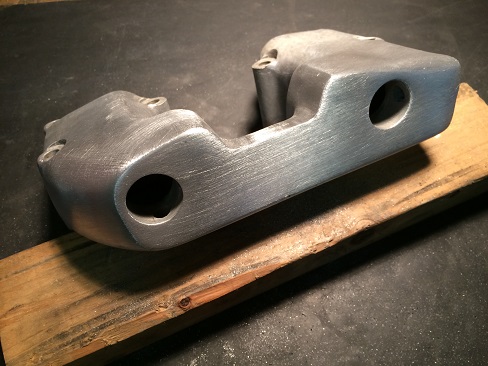
Take long, even strokes both ways. If the base metal isn't dead-flat, it will not produce a shine when polished.
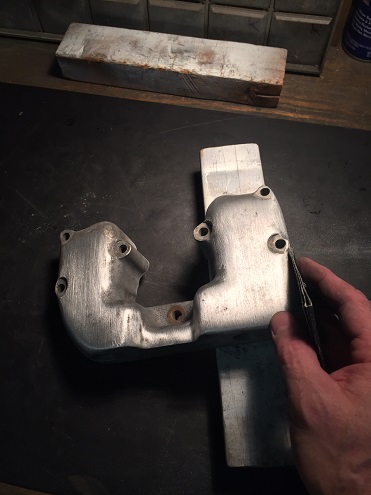
TIP: If you're getting blisters from sanding, you're probably pressing down too hard. If the paper you're using is not cutting, switch to a coarser grit.
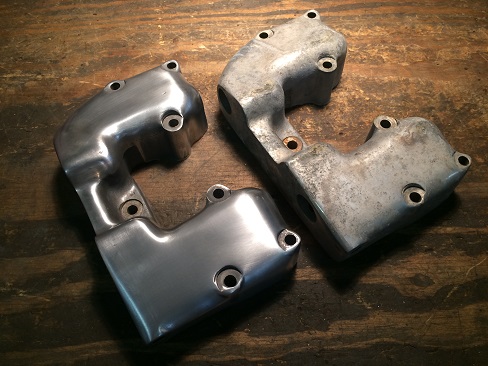
After the diagonal swipes are no longer visible, switch to fine Emory cloth.
Wet sanding with 240 grit paper should bring the aluminum to a flat, dull finish.
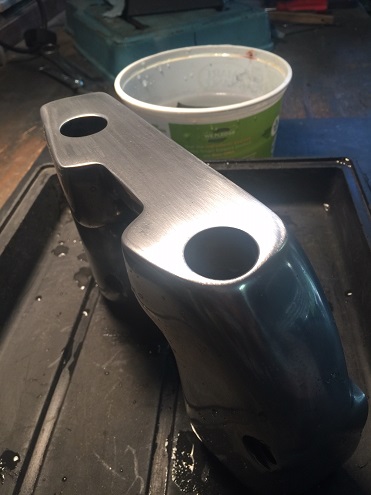
The aluminum is now ready for buffing.
************************
Buffing Wheels
Metal polishing can be done by hand, but a buffing wheel on a bench grinder is much faster.
There are many different styles and sizes of buffing wheels.

Buffing wheels are available in different diameters. Since my DIY sander is small, I use 6" buffing wheels.
Homemade Sander/Polisher
This DIY polisher is nothing more than an old electric motor fitted with an arbor.
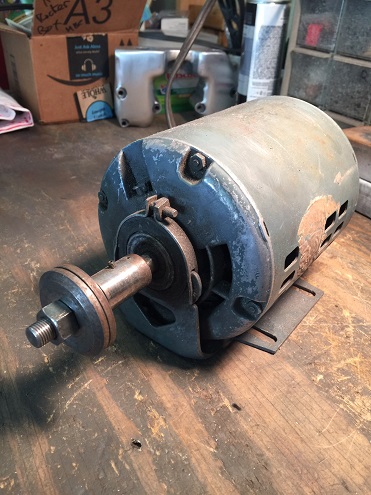
Drawbacks to a homemade polisher are, it only has one-speed and one arbor, so you'll be stopping to switch wheels quite often.
TIP: If you need more buffing wheel surface, you can mount two of the same wheels next to each other.
2024 Update: Grinder/Polisher
I found this used bench grinder locally at a moving sale, and added a buffing wheel to one side.
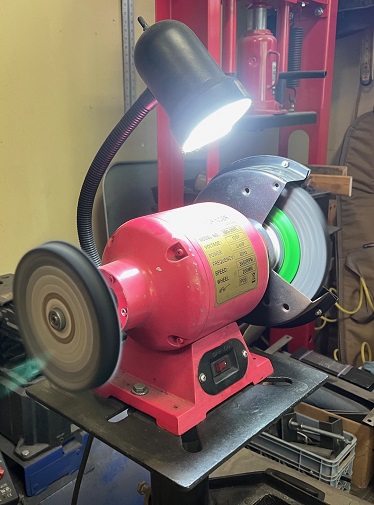
The motor spins at 3,300 rpm, which is a little fast for a buffing wheel. But as long as you're not polishing paint (particularly clearcoat) you'll be OK.
************************
Buffing Compounds
For aluminum, (brown) Tripoli cutting compound works best.
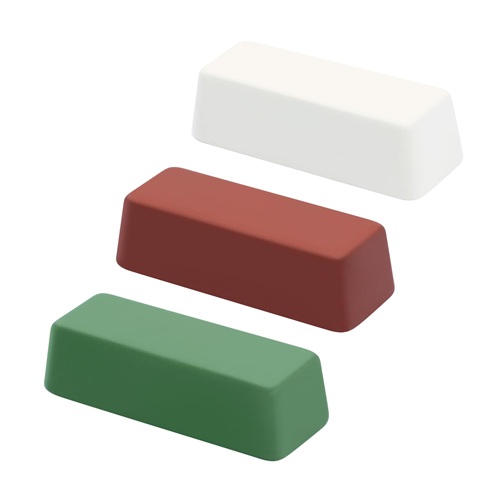
************************
Metal Polishing Kits are readily available that will include buffing wheels, compound, and 1/2" arbor.
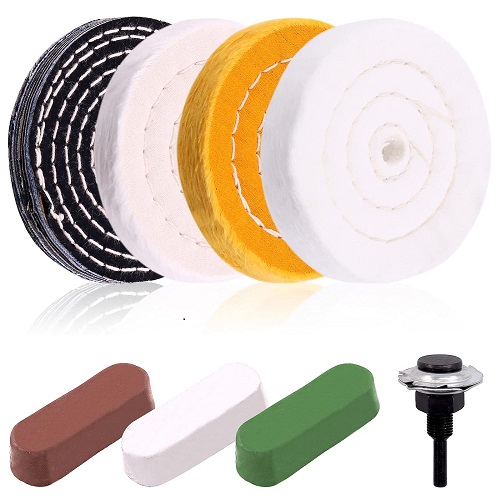
Shop: Metal Polishing Kit
************************
Should I Clear Coat Polished Aluminum?
On motorcycle forks and other parts that aren't exposed to engine heat, you can spray clear coat paint after the polishing is done. Personally, I've never had good results with clear coats looking good or lasting for any length of time. I'll leave the polished aluminum bare, then clean and polish when needed.
Conclusion
True, polishing aluminum engine parts is time consuming, but it's also very satisfying. It's almost relaxing. And it's a nice change of pace from other restoration tasks, such as rebuilding a bottom end or finding an electrical short.
************************
Other Aluminum Parts That Can Be Polished
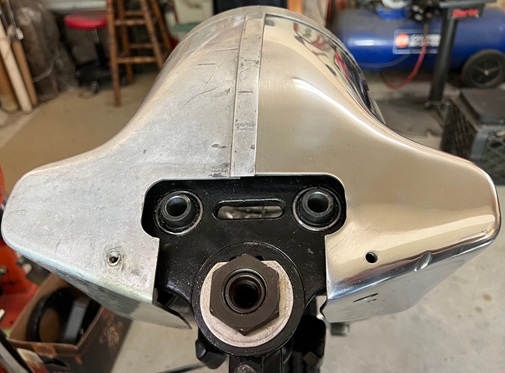
1961 Harley headlight nacelle, right side polished, left side unpolished.
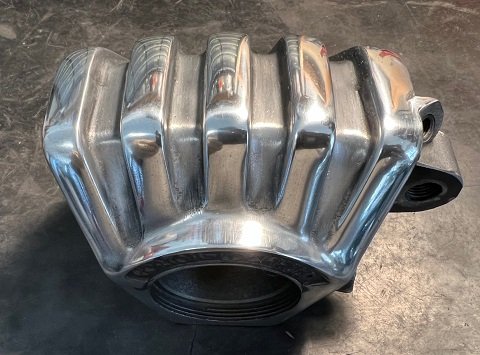
Norton Commando brake caliper after polishing
These vintage Corvette valve covers sat in storage for 20 years.
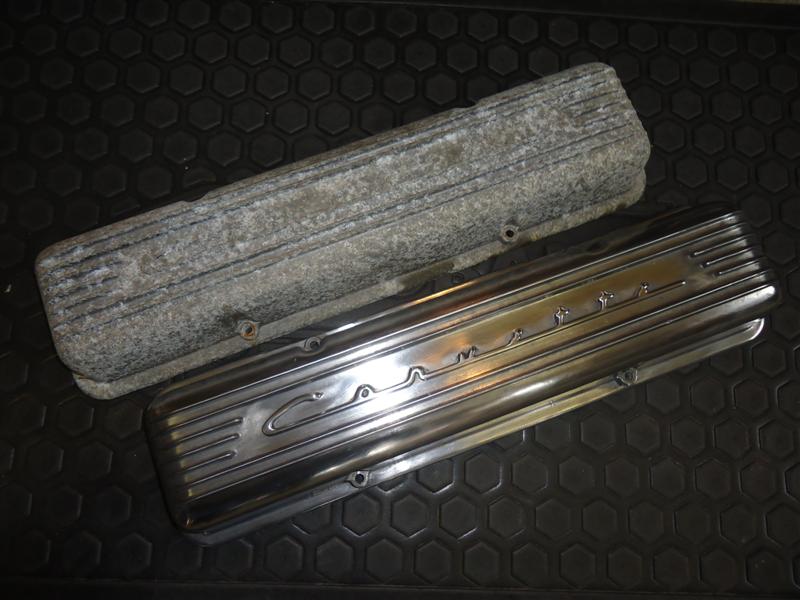
Aluminum Valve Covers Before and After Polishing
************************
Cleaning Aluminum
After several months, the lustre of the polished aluminum fades. To bring the shine back up; clean off any dust or dirt, scuff with a Scotch-Brite pad (fine, not coarse), then apply a small amount of polish.
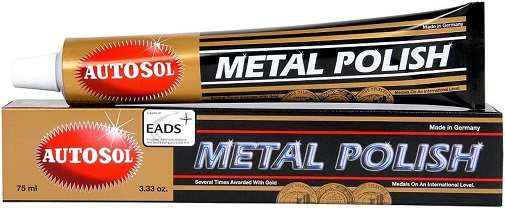
One of the best aluminum polishes on the market today is Autosol Metal Polish.
************************
Articles of Interest: